Before “Advanced SMPS Transformer design program” ExcellentIT and “Ir2153 SG3525 Frequency Calculation Programs for Switch mode power supplies with raisers”. SMPS transformer design tool (ver.4000) Here's a full and complex design tool for calculating the SMPS transformer based on a push-pull, half-bridge and full-bridge topology. It has many pop-up tips to help you to use it and correctly paste the values.
- Excellentit Smps Transformer Calculation Tool 7100
- Excellentit Smps Transformer Calculation Tool 7300
- Smps Transformer Calculation Tool 7100
- Excellent It Smps Transformer Calculation Tool 2017
- Excellent It Smps Transformer Calculation Tool
- Excellentit Smps Transformer Calculation Tool Free Download
Magnetic Builder (Magnetic Design Software, Inductor and Transformer design tool) | |
PowerEsim is a free web-based software providing power supply (SMPS) design, transformer design, magnetic design, loss analysis, thermal analysis, waveform analysis, MTBF analysis, BOM building, DVT analysis and optimization of power supply (SMPS). | |
Click to try PowerEsim (www.powerEsim.com) |
Excellent It Smps Transformer Calculation Tool 5,7/10 8308 reviews MMU offers various engineering courses in Biotechnology, Civil Engineering, Electrical Engineering, Computer Science Engineering etc. Apply now for admissions 2. I present to you my program for the calculation of transformers. In your theme SMPS transformer design tool. Are working on Excellent. Transformer Calculation v0.1 is program for calculating number of coils and wire thickness. If you have some experience in assembling transformers, then this program is perfect for you. If you don’t known anything about assembling transformers, please don’t use calculations from this program for building your own transformer!
What is magnetic builder (Inductor and Transformer design tool)?TopClick here to try Online Magnetics Builder (design tool) now
Magnetic Builder is a useful magnetic design software. It is a tool for user to create his/her own magnetic component (inductor and transformer) by selecting different ferrite core, bobbin type and winding method. Engineering drawing will be automatically produced to reduce user work load.
All the transformer and inductor built can be saved and reused onto a power supply, as long as the winding number are matched.
Inductor/Transfomer are necessary parts of switching power supply circuits.
The Advantages of Using Transformers
Transformers used with the three basic topologies offer certain advantages over the simple circuits introduced in the previous section. Namely:
Simple calculator to calculate coils of Transformer and Inductor
Download PFC Design Tool from Metglas
Output Inductor Design Tool from Metglas
Online Inductor Design Calculator Test
Online Current Transformer Design Software
Inductor and Flyback Transformer Design [PDF]
Inductor Design Procedure[PPT]
Filter Inductor Design Procedure[PPT]
Create a new transformer/inductorTopClick here to try Online Magnetics Builder (design tool) now
Click “Magnetic Builder” a “Number of Windings” page appear for user to first defining the number of primary winding and number of secondary winding.
Add number of primary and secondary windingTopClick here to try Online Magnetics Builder (design tool) now
The number of primary winding and number of secondary winding can be change. The default value is one.
Add BifilarTopClick here to try Online Magnetics Builder (design tool) now
- Move cursor to the winding
- The winding will turn RED
- Click on the winding and you can see the picture as below
- Winding with the same number of turn will be shown and can be selected for bilfilar.
Flux BandTopClick here to try Online Magnetics Builder (design tool) now
Click the button “Flux Band”
Two type of flux band are supported. Click the checkbox to add the flux band.
After clicked the checkbox, the core with the flux band can be preview. The Flux band thickness and width can be set.
Add Primary / Secondary WindingTopClick here to try Online Magnetics Builder (design tool) now
Extra Winding can be added by clicking “Add Pri Wdg” or “Add Sec Wdg.” The usage of this feature is recommended for non-operating winding only. User is recommended to preset the proper winding number at the “Number of Windings” page.
Faraday ShieldTopClick here to try Online Magnetics Builder (design tool) now
The user can change a particular winding to Faraday Shield. Only extra windings can be changed to Faraday Shield.
Add a transformer/inductor to the designTopClick here to try Online Magnetics Builder (design tool) now
After creating a new transformer/inductor, you can add it to the design by pressing “Add Component”.
When the transformer/inductor is added, the message with transformer's designator is shown.
Make split winding or parallel winding TopClick here to try Online Magnetics Builder (design tool) now
User can “Split” a winding to several section by choosing from “No. of windings” or Parallel Winding in any winding for sandwiching winding method.
Customize the winding orderTopClick here to try Online Magnetics Builder (design tool) now
The winding order can be changed by the list box. W1 means the most inner layer.
Adjust number of turns for each winding TopClick here to try Online Magnetics Builder (design tool) now
The number of turns for each winding is shown in the blue button. You can press this button to modify the number of turns.
Select the wire used for each winding TopClick here to try Online Magnetics Builder (design tool) now
The wire information for each winding is shown in the blue button. It shows the Wire name and the number of parallel wires. You can press this button to modify it.
Every change can affect the total lossTopClick here to try Online Magnetics Builder (design tool) now
The “Total Loss” means the overall losses of the power supply and is shown at the top of the interface and will be automatically updated for any changed in transformer design.
Every change can affect transformer/inductor lossTopClick here to try Online Magnetics Builder (design tool) now
The “Transformer Loss” means the losses of the whole transformer and is shown at the top of the interface and will be automatically updated for any changed in transformer design.
Some change can affect the Peak FluxTopClick here to try Online Magnetics Builder (design tool) now
The “Bm” means the peak flux density of the transformer and is shown at the top of the interface and will be automatically updated for any changed in transformer design.
Putting transformers in parallel / series TopClick here to try Online Magnetics Builder (design tool) now
You can clone the current transformer and produce a set of transformer and place them in parallel or in series.
Changing the transformer/inductor inductanceTopClick here to try Online Magnetics Builder (design tool) now
Inductance value is shown in the interface. On the left there is a blue button which can be used to modify the inductance.
Select different core shape and manufacturer TopClick here to try Online Magnetics Builder (design tool) now
Information on the selected core and selected magnetic materials is shown. You can press the blue button to change it.
Select different core materialTopClick here to try Online Magnetics Builder (design tool) now
After you press on “Core Shape”, you can see the following page.
You can click on “Core Material” button on the bottom right to select different core material.
Overall bobbin thickness can be adjustedTopClick here to try Online Magnetics Builder (design tool) now
Overall bobbin thickness is a short cut to change all the left, upper and lower bobbin thickness at once.
Adjust the overall creepage tape width TopClick here to try Online Magnetics Builder (design tool) now
Overall creepage tape width is a short cut to change all the upper and lower creepage tape widths in all winding.
Adjust the Overall winding indentTopClick here to try Online Magnetics Builder (design tool) now
Overall Winding Indent is a short cut to change all the winding indents in all winding.
Adjust the Overall Multi-Layer Winding settingTopClick here to try Online Magnetics Builder (design tool) now
Overall Multi-Layer Winding is a short cut to change all the Multi-Layer Winding property.
Change the No. of wire in parallelTopClick here to try Online Magnetics Builder (design tool) now
After you select the wire (section 7.8.12), you can see the above page.
Adjust the overall wire used in all windingTopClick here to try Online Magnetics Builder (design tool) now
There is a shortcut button “Change All wire” that can change the wire for all winding by one step only.
How to change the Winding Wizard option?TopClick here to try Online Magnetics Builder (design tool) now
After you press the button “Winding Wizard”, you can see the following page and set the winding wizard option.
The check box in the “Winding Wizard” page provide a list of allowable background actions when the wire winding area is bigger than the allowable winding window area.
Change bobbin thickness on each side TopClick here to try Online Magnetics Builder (design tool) now
After press the button “Bobbin Setting”, then you can see
All four side of the bobbin can be individually adjusted.
Configure the bobbin winding window dimension TopClick here to try Online Magnetics Builder (design tool) now
After press the button “Bobbin Setting”, then you can see
How to change the winding layer usage?TopClick here to try Online Magnetics Builder (design tool) now
After press the button “Bobbin Setting”, then you can see
The winding layer usage is the usage ratio between the allowable bobbin height and Inner Bobbin height.
Bobbin with split wallsTopClick here to try Online Magnetics Builder (design tool) now
After press the button “Bobbin Setting”, then you can see
User can choose Vertical or Horizontal type of split wall.
Configure number of split wallsTopClick here to try Online Magnetics Builder (design tool) now
After press the button “Bobbin Setting”, then you can see
User can design number of split walls by choosing from “Select No. of Split Walls”
Configure the thickness of split walls TopClick here to try Online Magnetics Builder (design tool) now
After press the button “Bobbin Setting”, then you can see
User can design the thickness of the split wall by choosing from “Thickness of Split Walls”
Configure the thickness of each partitionTopClick here to try Online Magnetics Builder (design tool) now
If you set more than 1 split walls in section 'Configure number of split walls', you can see
User can design the individual window height of each partition by clicking the arrows to increase or decrease partition thickness.
Configure tape characteristic in each winding TopClick here to try Online Magnetics Builder (design tool) now
After pressing the button “Winding Construction”, user will see the “Advance Winding Construction” page
Basically each copper winding has its inherent tape winding for insulation. If no insulation is need set No. of layer to 0.
Configure the tape thickness of each winding TopClick here to try Online Magnetics Builder (design tool) now
The thickness of tape can be set by changing the value of “Thickness (mm)”
Configure the number of layer in each winding TopClick here to try Online Magnetics Builder (design tool) now
The no of turn of the tape can be set by changing the value of “No. of Layer”
Configure the tape type used in each windingTopClick here to try Online Magnetics Builder (design tool) now
The material of the tape can also be set by “Type”
Configure the dot sign of each windingTopClick here to try Online Magnetics Builder (design tool) now
User can choose whether the dot sign is lie with winding started at the “Winding Start at Dot Sign” box.
Define the winding start position of each winding TopClick here to try Online Magnetics Builder (design tool) now
User can choose the winding start position at the “Winding Start Position” box.

Configure the winding indent of each winding TopClick here to try Online Magnetics Builder (design tool) now
User can choose how the wire is packed at the “Winding Indent” box.
Distributed – wire will evenly wind in the allowable winding height.
Center – wire will be packed tight at center of the allowable winding height.
Low – wire will be packed tight at lower part of the allowable winding height.
Upper – wire will packed tight at the upper part of the allowable winding height.
Configure the characteristic of multi-layer winding of each winding TopClick here to try Online Magnetics Builder (design tool) now
User can choose how the wire is arranged if more than 1 layer is needed to complete the winding in the “Multi-Layer Winding” box
Shared – wire will evenly shared in each layer
Tight – wire will be just tightly wind.
Creepage positionTopClick here to try Online Magnetics Builder (design tool) now
User can choose how the creepage tape is placed in the “Creepage Position” box
End-To-End – Creepage tape will placed at both end of the allowable winding height
Tight – Creepage tape will placed just beside the wire.
Creepage width of each windingTopClick here to try Online Magnetics Builder (design tool) now

User can choose how the width of the creepage tapes by changing “Upper Creepage Width” or “Lower Creepage Width” box.
Change the number of turns of each split windingTopClick here to try Online Magnetics Builder (design tool) now
If more than 1 split sub-winding are made (section 7.8.9), you can change the number of turns of the each split winding by changing “No. of Turn” box.
Locate the winding in which bobbin partitionTopClick here to try Online Magnetics Builder (design tool) now
If more than one partition (section 7.8.31 & 7.8.32), user can locate the winding in any partition by changing “Winding’s Partition” box.
Generate Transformer/Inductor DrawingTopClick here to try Online Magnetics Builder (design tool) now
After pressing “Generate Drawing”, user can fill in all the detail information for making a professional transformer drawing.

Designed parameters of a transformer/inductorTopClick here to try Online Magnetics Builder (design tool) now
User can fill in checking parameter, e.g. DC resistance, Magnetizing Inductance and Leakage Inductance, for IQC. Once the check box is clicked, the value between the corresponding pins is enabled for inspection. Simulated value is recommended but user can change the actual IQC specification by change wording in the corresponding text box.
Change the testing details of Transformer/Inductor DrawingTopClick here to try Online Magnetics Builder (design tool) now
User can fill in the testing details in the bottom of Transformer Drawing interface.
Different type of bobbin can be selectedTopClick here to try Online Magnetics Builder (design tool) now
User press “Select Bobbin” at the top-right side and will see the following page.
Click on the picture to select bobbin type
Change the number of pins of bobbin TopClick here to try Online Magnetics Builder (design tool) now
User can change the number of pins of bobbin there.
Add/ delete fly pinsTopClick here to try Online Magnetics Builder (design tool) now
In “Generate Drawing” page (section 7.8.44), user press “Add Fly Pins” at the top-right side and user can see the following page.
User can add or delete fly pins pressing corresponding button
Configure details of fly pins TopClick here to try Online Magnetics Builder (design tool) now
After adding fly pins (section 7.8.44.5), you can modify the detail of the fly pin or delete the corresponding fly pin by pressing “X”.
Define the termination pins of a winding TopClick here to try Online Magnetics Builder (design tool) now
Press the number button can open an interface that can define the termination of a winding.
User can click one or more of the pins or fly pins available.
Preview the Transformer/Inductor drawing page TopClick here to try Online Magnetics Builder (design tool) now
The 'Preview' button at the bottom can open a preview page of the transformer drawing.
Home |
Introduction |
Loss Analysis |
Waveform analysis |
Closeloop Analysis |
Thermal Analysis |
Life & MTBF |
BOM Builder |
DVT(4 Corner) Report |
Transformer Design |
Circuit Optimization |
Download resources |
EE reference |
Transformer Design |
Terms of use |
Help Manual |
Copyright © 2021. PowerELab Limited. All rights reserved. |
An SMPS transformer becomes apparent at the output of all forward-mode converter. Converters applying the forward, push-pull, half-bridge and full-bridge topologies are typically forward-mode converters. Therefore, calculation of the output inductance employs the equivalent techniques for any 4 of these kinds of widely used topologies. The actual intent behind the output inductor is always to retain power for the load in the period just about every switching cycle whenever the power devices (BJTs, MOSFETs or IGBTs) are switched off. The electrical operation of the SMPS transformer is always to combine the rectangular switching pulses (pulse width modulated signals with changing duty cycle) into DC. The capacitor positioned after the inductor smooths the DC into ripple free DC.
The calculation of the SMPS transformer is pretty straightforward. More often than not, a self-gapped toroid core can be used. Gapped ferrite cores (the types employed for ferrite transformers, eg ETD39) may possibly be accustomed without problems.
The formula for determining the output inductance is:
L(min) = [Vin(max) - V(out) x T(ON) / 1.4 x Iout(min)
Vin(max) = maximum voltage next to the output rectifier within that specific output.
Vout = output voltage.
Toff(est) = anticipated ON time of power device at the maximum input voltage.
Iout(min) = least heavy anticipated load current to achieve that output.
Excellentit Smps Transformer Calculation Tool 7100
Determined from the above formula is L(min) which is the minimal recommended inductance, below which the core is going to be drained of flux at the least rated load current for that specific output.
Make sure you plan a circuit that permits for functioning without having any load. Unquestionably, you can not replace zero for Iout(min) because that might contribute to an L(min) figure of infinity. And surely, that actually isn’t imaginable, could it be?
Which means that, what you need to accomplish is that you ought to decide upon the very least permissible current.
Work with a resistor load along at the output of the power source in order that should you have hardly any load, this resistor load delivers the bare minimum load.
Iout(min) needs to be significant enough that L(min) certainly is not exceedingly big; it additionally should not be exceedingly massive which may induce excessive power deficits, therefore a negative efficiency, on account of the power dissipation in the output resistor.
Commonly, this resistor is termed a dummy load whose exclusive objective is always to offer the minimal load if there is hardly any other load at the output of the converter / supply of power.
Seeing that we understand the minimum needed inductance, we should comprehend the number of turns to incorporate on our core.
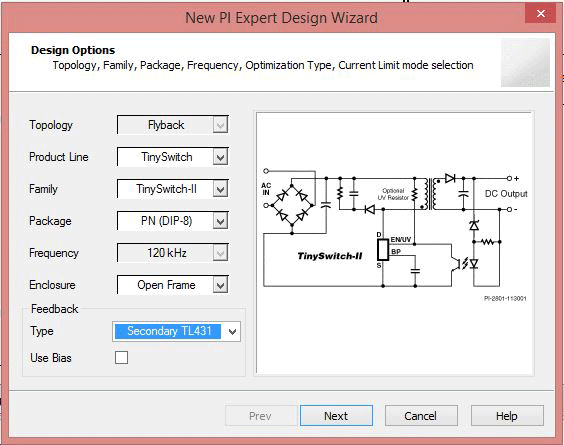
Through the datasheet of the core, you will discover the AL magnitude. This signifies the inductance upon each turns squared:
AL = L/N^2
L will be the inductance and N would be the amount of turns. Implementing M as the argument:
L = √ L/AL
Thus, here is the formula which may be utilized to figure out the quantity of turns when we identify the preferred inductance.
Occasionally you probably will not be familiar with the AL valuation. You possibly will not find out the component spec the core you own thereby unable to identify the datasheet.
No matter what the explanation, it is possible to experimentally identify the AL valuation.
Execute several turns and determine using an L meter, the inductance. After that, measure the inductance for a sets of many different number of turns.
Do it again for all these selected numbers of turns. Therefore, determine the inductance for, as an example, 5, 10, 20, 40 turns after which for each and every, determine the AL value. Obtain the average AL value.
One of the things that can be done is, you might sketch a graph of L against N2. The gradient of the most effective match line could possibly be the AL value. You might also mathematically determine the gradient of the “regression line”. Exercise whatsoever course you realize is the quickest.
At this moment let’s check out a case in point to solve just what you’ve understood until at this instant.
Excellentit Smps Transformer Calculation Tool 7300
Let’s stipulate that our converter is a half-bridge converter.
The input voltage for the converter will be different out of 150VAC (212VDC) to 250VAC (354VDC). Output voltage from the converter can be 14VDC. The turning frequency is 50kHz.
Transformer primary: 26 turns
Transformer secondary: 4+4 turns
The formula for computing the minimal essential inductance is:
L(min) = [Vin(max) - V(out) x T(ON) / 1.4 x Iout(min)
We will have to evaluate the output voltage with the transformer secondary at 354VDC input, that may be our optimum input voltage.
We’ll believe that the voltage drop as a result of the rectifier diode is 1V. Consequently the typical output voltage within the transformer secondary is 15V. Transformer turns ratio (primary: secondary) = 26:4 = 6.5
Thus, at any time typical secondary voltage is the same as 15V, typical voltage across transformer primary is 6.5 * 15V = 97.5V. In case duty cycle was 100%, voltage across transformer primary could well be 177V (50% the DC bus voltage - consider half-bridge topology). Therefore, the duty cycle is (97.5/177)*100% = 55%.
Average output voltage on transformer secondary will be 15V which has a duty cycle of 55%. Consequently, maximum output voltage is 15V/0.55 = 27.3V, and then there is assumed a diode reduction of 1V. Therefore, Vin(max) is 26.3V.
At optimum input voltage, duty cycle will probably be smallest. This can be any time the off time is going to be the greatest.
We now have determined a duty cycle value of 55% - this is actually the minimum duty cycle number. Since switching frequency is 50kHz, period of time is 20µs. The off period is 0.45 * 20µs = 9µs. Which is our Toff(est).
Let’s stipulate that the particular minimal load is going to pull 500mA current. Using a 14V output and 500mA current, the electricity dissipated in the output resistor will likely be:
P = VI = 14 x 0.5 W = 7 Watts
That is certainly a great deal of power! In case it’s agreeable, by all means employ a 500mA minimum load. If you decide to fetch the minimum load all the way down to 250mA, you trim down power dissipation (above) to 3.5W.
Therefore now we have figured out all the essential variables. Let’s connect these into the formula.
L(min) = (26.3 - 14) x 9 x 10^-6 / 1.4 x 0.25
Smps Transformer Calculation Tool 7100
= 316uH
This is often the bare minimum expected inductance. Feel free to use an inductance higher than the minimum number established, considering that, well you determined the minimum essential inductance.
Let’s believe we’ll exploit an inductance of 450µH. Let’s stipulate that we’ve picked out a toroid core with an AL valuation on 64nH per turn squared.
To begin with, the expected inductance is 316µH that could be equivalent to 316000nH.
Excellent It Smps Transformer Calculation Tool 2017
Therefore the preferred range of turns is:
Excellent It Smps Transformer Calculation Tool
It can be possibly 70 or 71 turns. This is often for 316µH.
Excellentit Smps Transformer Calculation Tool Free Download
Regarding 450µH:
Let's make this around 84 turns.
So...now you know How to Calculate SMPS Transformer Turns at home, which you can apply this easy solution in order to determine the necessary output inductance for any converter in which employs the forward, push-pull, half-bridge or full-bridge topology. It’s effortless and also Lets hope I have personally had the opportunity to enable you to comprehend without a doubt. I want to appreciate your feedback and opinions!